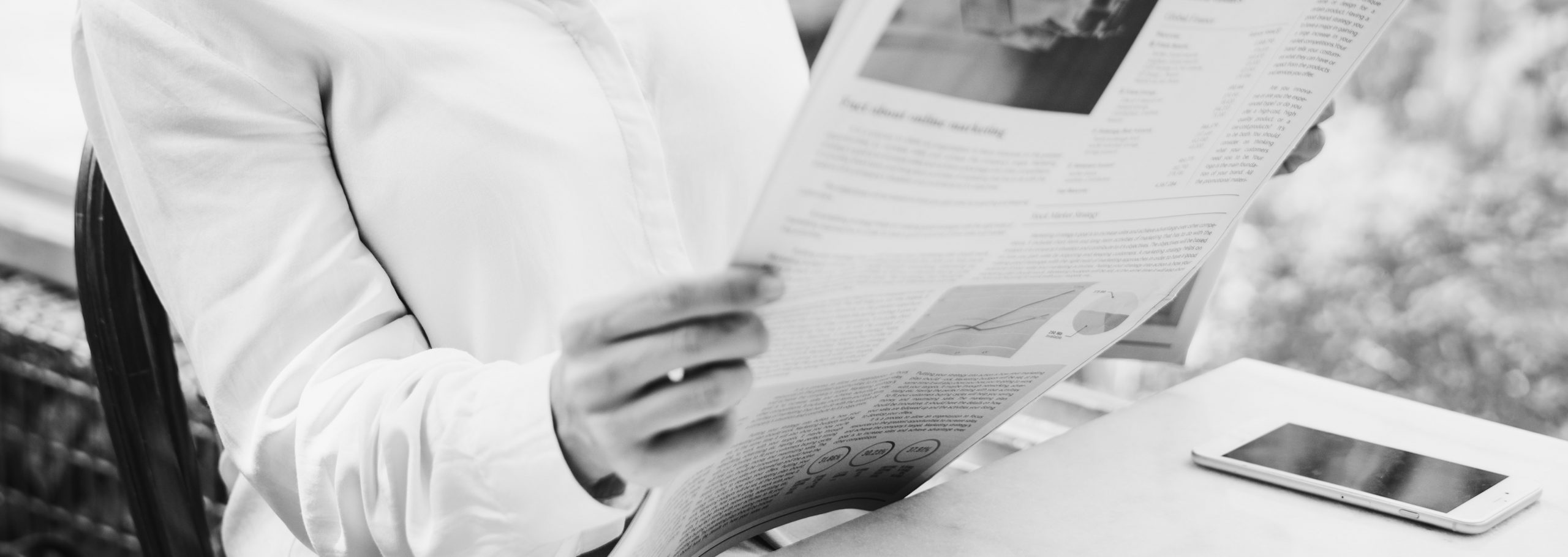
Rethinking Design with Engineering Plastics: When and Why to Replace Metal in Industry
Replacing Metal Components with Engineering Polymers Is No Longer a Trend—It’s a Competitive Advantage. Discover the benefits, key criteria, and how to approach the transition effectively.
Why Replacing Metal with Engineering Polymers Is No Longer Just a Trend
In industries such as automotive, industrial machinery, electronics, and aerospace, the replacement of metal with high-performance engineering plastics has evolved from an emerging innovation into an established practice. This shift is driven not only by cost-reduction goals but also by regulatory pressures, sustainability targets, and increasingly demanding technical requirements.
Choosing high-performance polymers is no longer merely a matter of material substitution—it’s a strategic design tool that enhances product efficiency, aligns production with ESG criteria, and boosts competitiveness.
When Does It Make Sense to Replace Metal with Engineering Plastics?
Not every metal part is a suitable candidate for replacement. The most effective way to identify opportunities is through a techno-economic lens. A component is ideal for substitution if it meets at least three of the following criteria:
Technical Criteria for Replacement:
- Features complex geometries that are difficult to machine.
- Requires mechanical strength, impact resistance, or corrosion resistance.
- Is part of systems where weight directly affects performance (e.g., moving parts).
- Is produced in medium to high volumes, making mould investment cost-effective.
- Is currently manufactured using energy-intensive processes such as casting or machining.
- Falls under sustainability, recyclability, or carbon footprint reduction targets.
What Are the Benefits of Replacing Metal with Engineering Plastics?
The advantages go beyond cost savings. In many cases, functional performance and durability are also improved. Key benefits include:
Weight Reduction
Up to 70% lighter than metal, improving energy consumption, transport efficiency, and system ergonomics.
Enhanced Specific Strength
Many engineering polymers outperform traditional metals in strength-to-weight ratio, making them structurally efficient materials.
Maintenance-Free Durability
Polymers don’t corrode or oxidise and are resistant to a wide range of chemicals—reducing operational costs and downtime.
Design Flexibility
Enable integration of multiple functions into a single part, with complex 3D geometries and in-mould aesthetic finishes.
Production Cost Savings
Shorter processes, no need for secondary operations (e.g., deburring or welding), and lower energy consumption.
Sustainability and Regulatory Compliance
Lower carbon footprint and alignment with regulatory frameworks such as:
REPowerEU
ESPR (Ecodesign for Sustainable Products Regulation)
How to Ensure a Successful Transition?
Replacing metal with engineering plastics is not a superficial change—it requires a clear methodology to ensure success from design through to production.
Key Stages in the Substitution Process:
- Candidate Identification – Techno-economic analysis to identify viable components.
- Material Selection – Choosing the right polymer or compound based on structural, thermal, and regulatory requirements.
- Functional Validation – CAE simulations, physical prototyping, and lab testing.
- Industrialisation – Mould design and manufacturing, supplier selection, and production ramp-up.
- Optimisation and ROI – Life Cycle Assessment (LCA), Return on Investment (ROI), and access to incentives.
In an industrial landscape increasingly shaped by energy efficiency, sustainability, and regulatory pressure, material selection is no longer a secondary decision—it’s a strategic lever.The replacement of metal components with engineering polymers is no longer an emerging trend—it’s a proven practice in sectors such as automotive, industrial machinery, electronics, and aerospace. Why? Because it enables redesign without compromising performance, optimises processes, and reduces costs.
At Plastibor, we bring extensive experience in redesigning and adapting metal parts to plastic, helping companies across various sectors optimise their processes, reduce costs, and enhance product efficiency. If your company is exploring this transition, we’d be delighted to support you with tailored solutions and a technically specialised approach.
Featured News
Rethinking Design with Engineering Plastics: When and Why to Replace Metal in Industry
Replacing Metal Components with Engineering Polymers Is No Longer a Trend—It’s a Competitive Advantage. Discover...
Discovering Pronutec’s Vertical Triple-Pole Fuse Bases: Innovation and Efficiency
At Plastibor, we are proud to collaborate with Pronutec, one of our key clients and,...
Renewable Solar Energy Project
Committed to the promotion of renewable energy, sustainability and environmental care. We welcome the...
